Installation of municipal Supply Bore Network
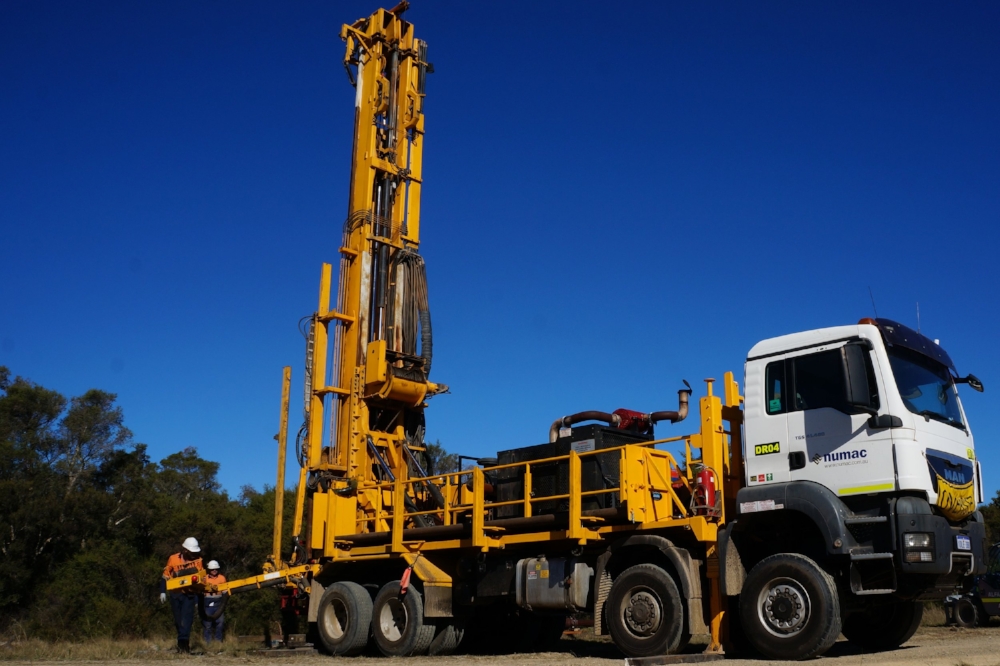
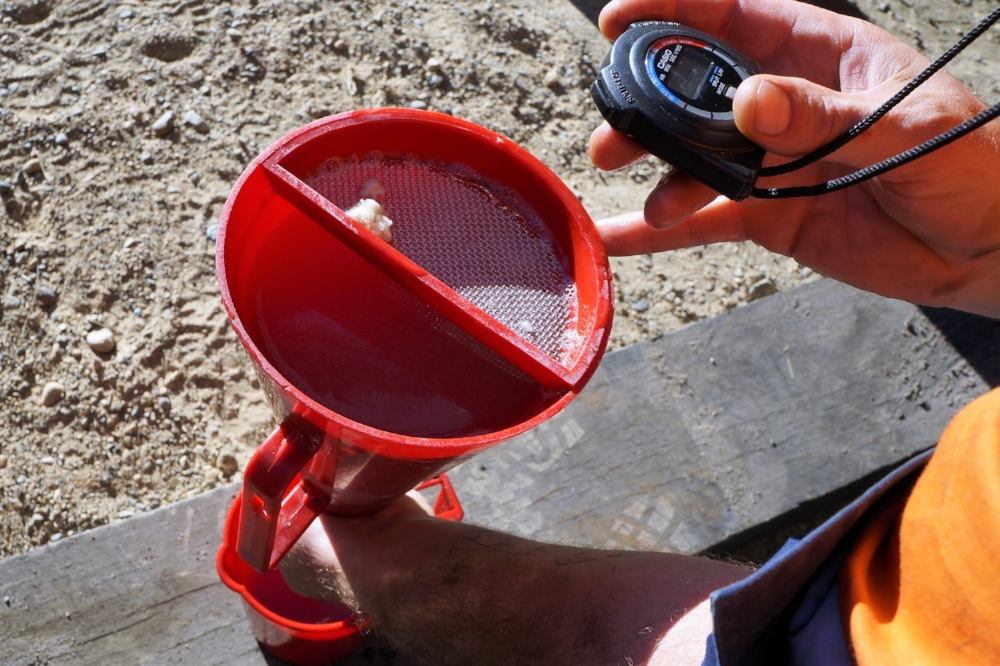
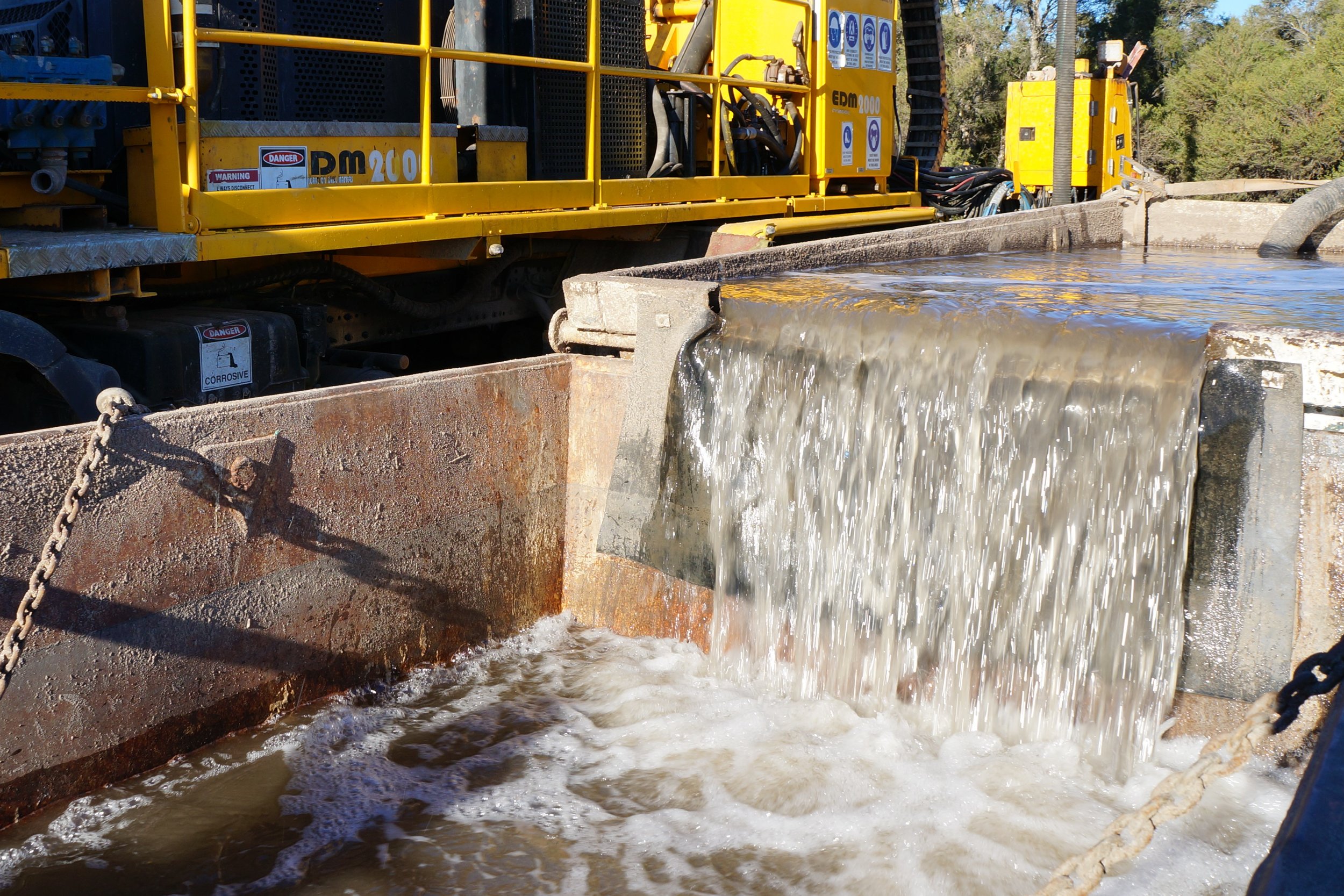
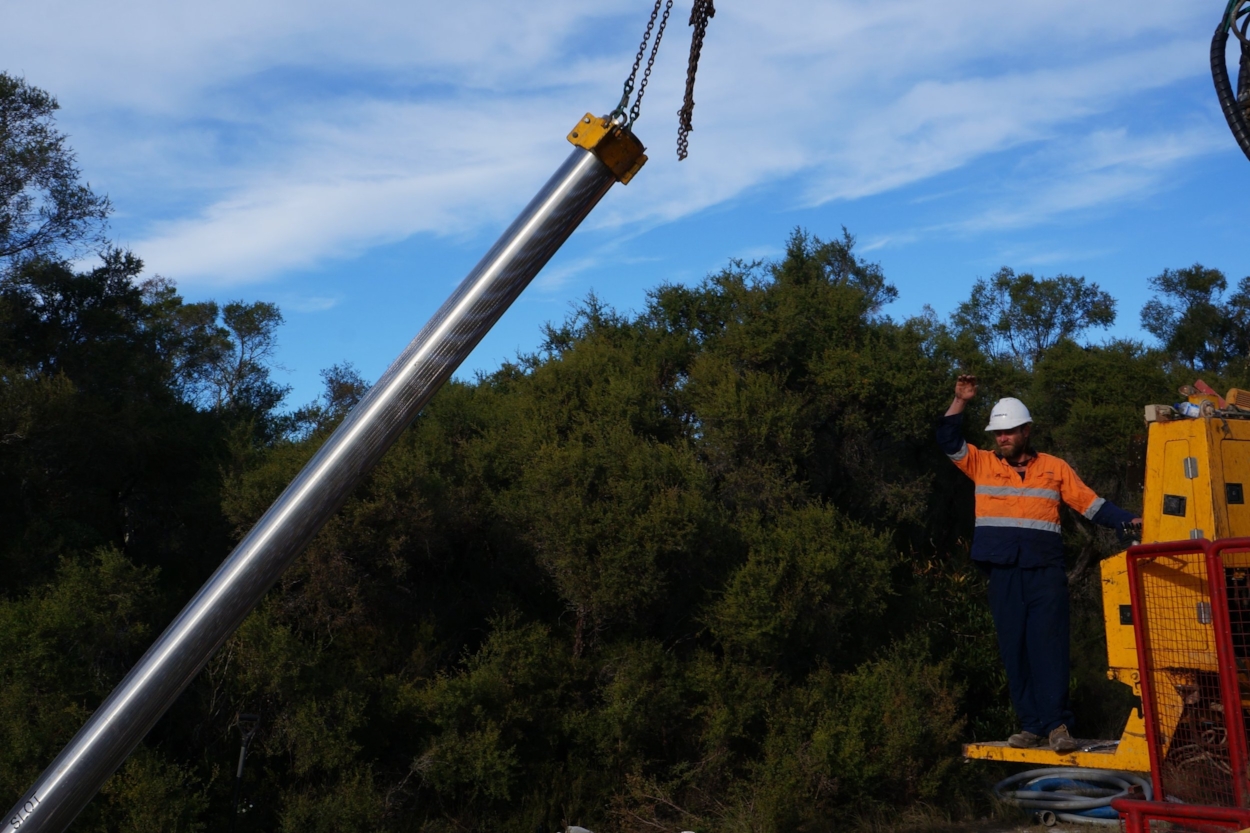
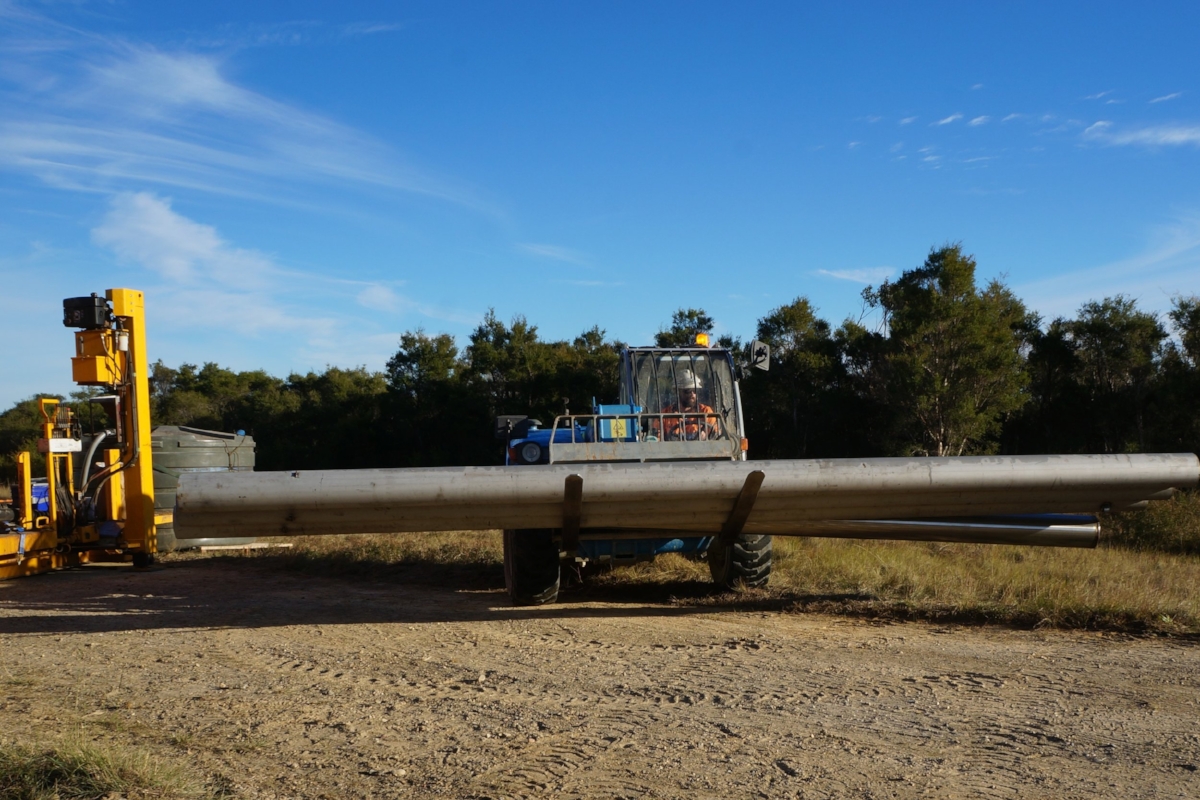
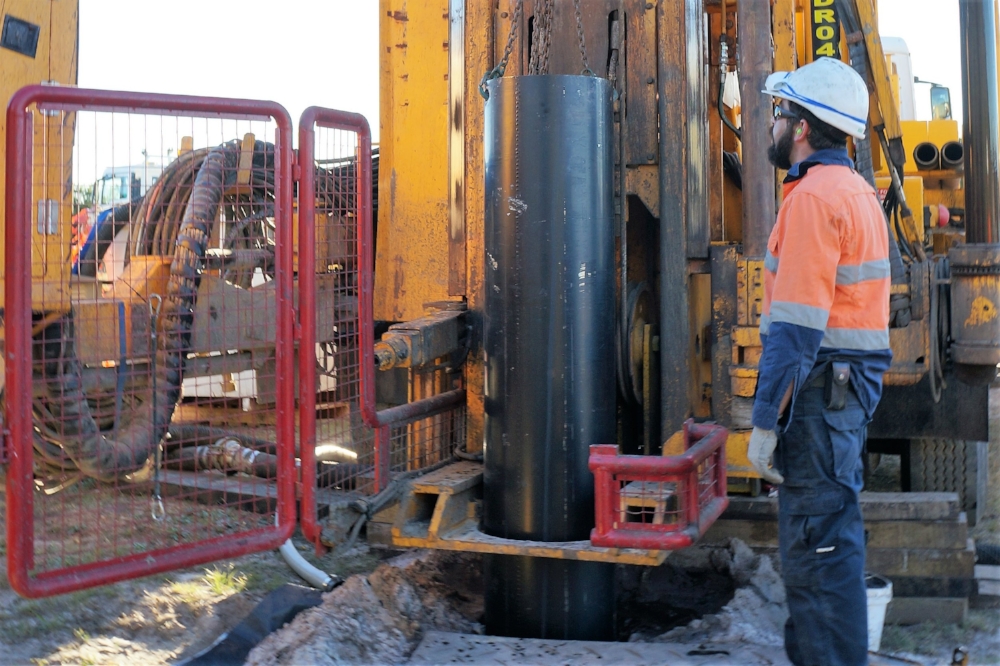
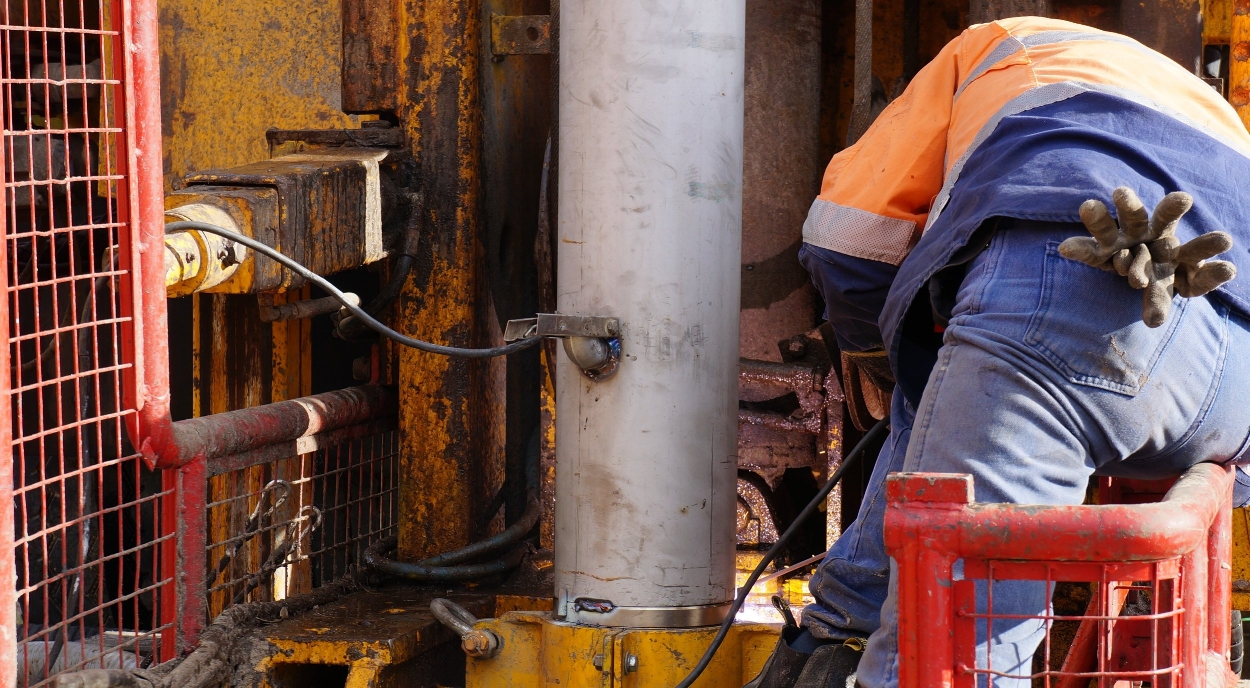
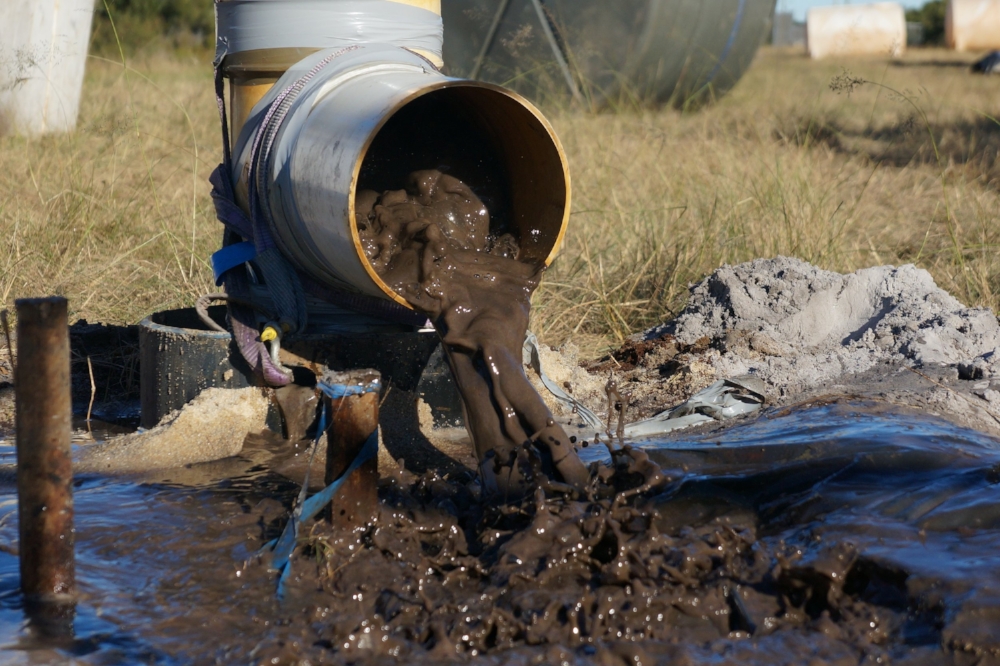
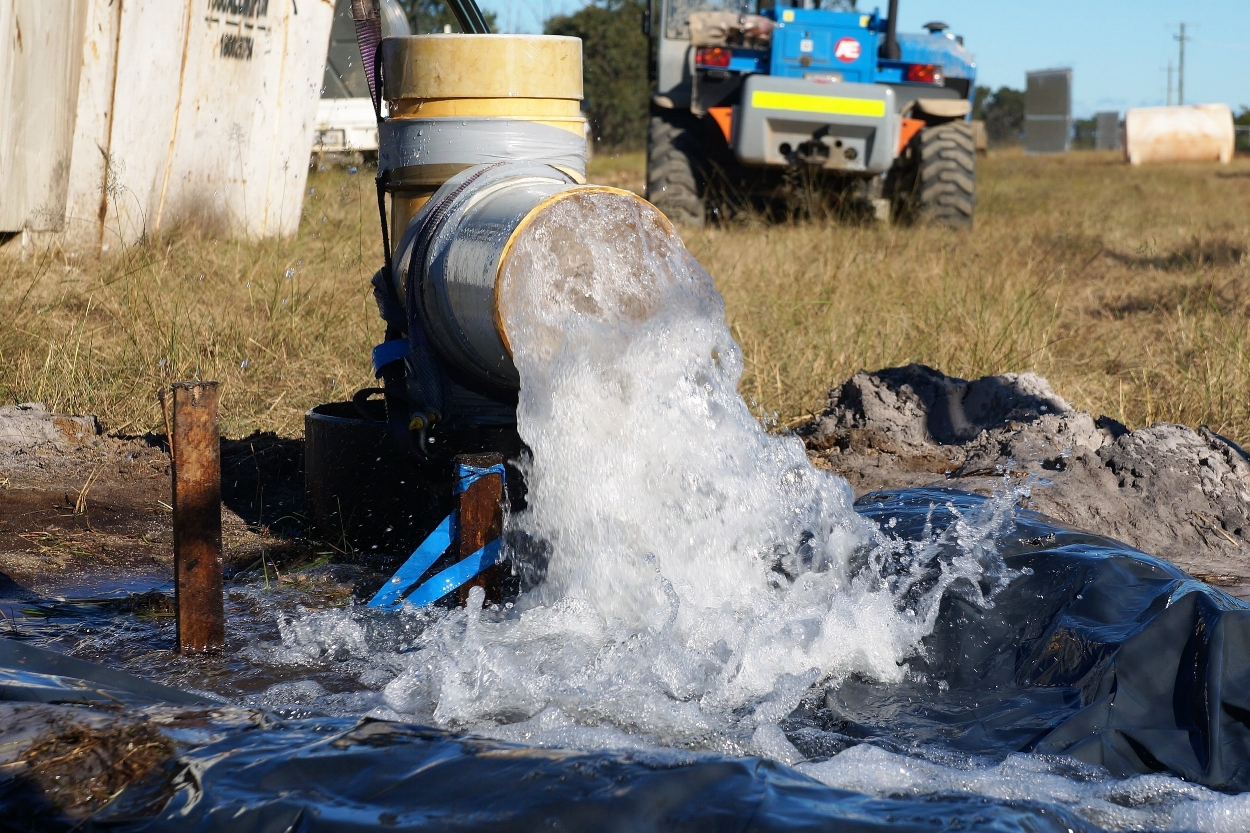
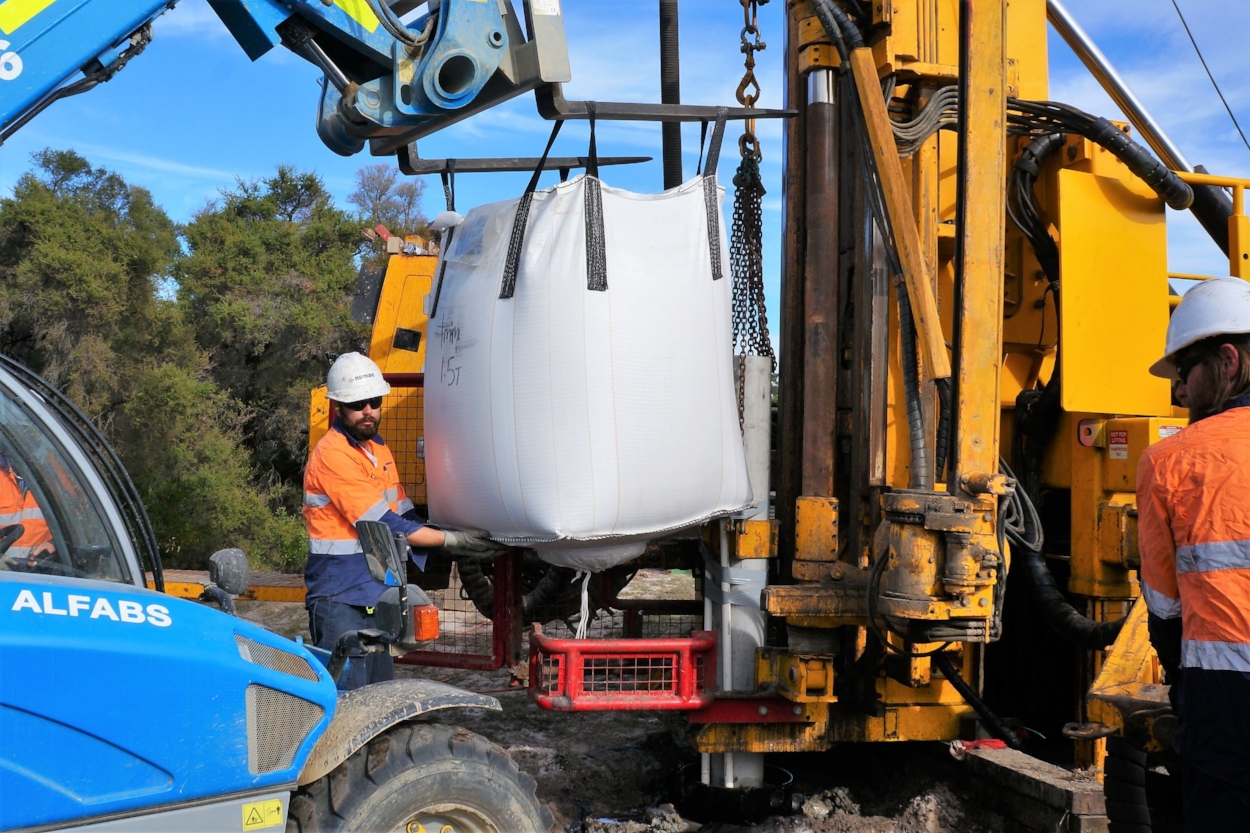
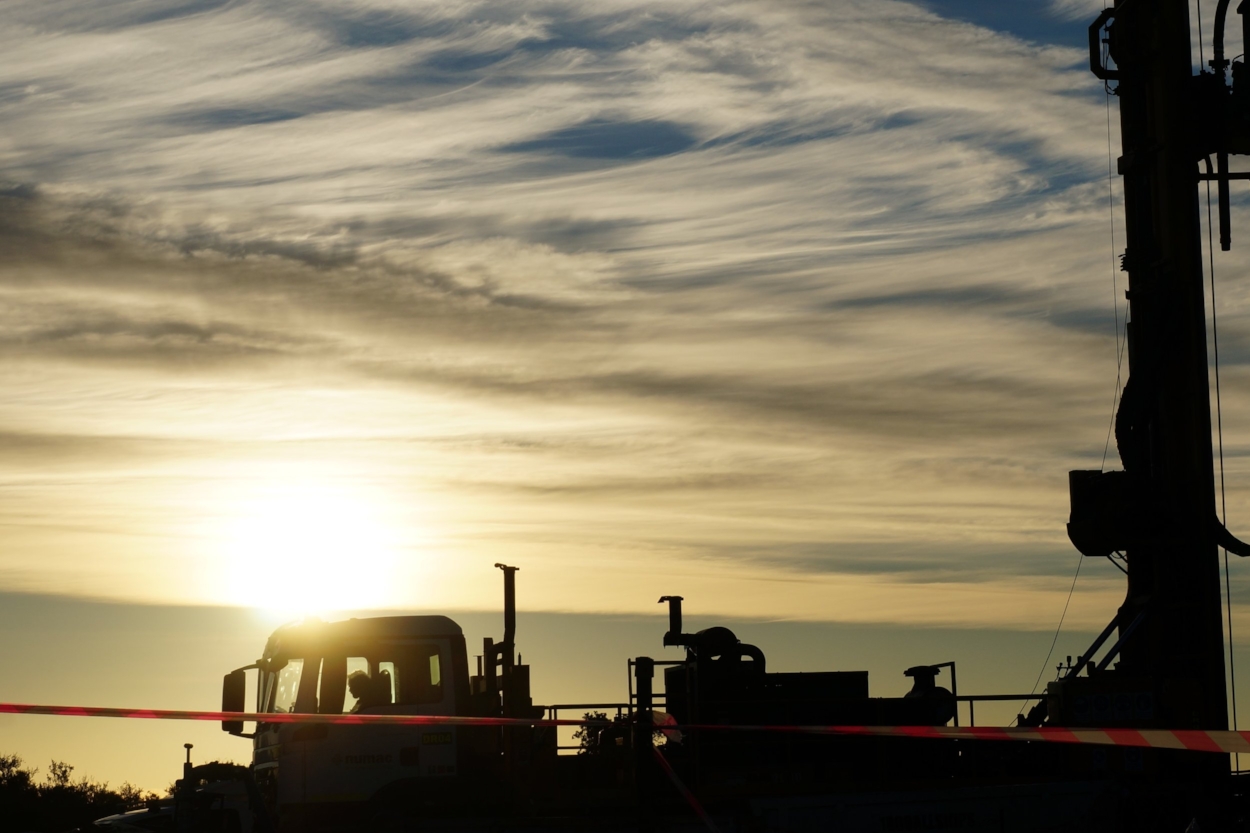
Upgrade of Municipal Supply Bore Network
Numac Drilling Services Australia was awarded a public tender by Hunter Water to manage and execute the drilling and installation of a network of 15 municipal water production bores and 12 groundwater monitoring bores within the existing use regional aquifer. The targeted underground water source located outside of Newcastle provides approximately 20 per cent of the lower Hunter’s drinking water. Just outside Newcastle NSW.
Overall the project was executed flawlessly. The 15 production bores and associated monitoring wells were all installed without downtime or incident. Pump testing on the completed bores confirmed impressive flow rates with potential daily production of up to 20 megalitres from the network.
In the contractor performance evaluation, the Hunter Project Manager states:
“In my opinion Numac Drilling services has been exceptional in achieving completion well within the required timeframes. Numac has managed quality, safety and environmental requirements adequately. The relationship with Numac has been really good. Numac has been open and honest in their dealings with Hunter Water. Numac has worked with Hunter Water to achieve quality outcomes. They are highly recommended for future works.”
Perhaps surprisingly, this was a first for Numac, to be engaged as the principal contractor on a project of this magnitude. It was equally a thrilling and daunting opportunity for the entire team. The full scope of the program and deliverables included; project management, health safety and environment, site operations management, procurement and management of multiple contractors.
Pre-mobilisation activities, site supervision, and program deliverables included; a safety management plan, comprehensive project and plant risk assessment, environmental management plan, site scouting, underground utility location, drill pad preparation, access track upgrades, traffic management, lithologic logs, gamma and neutron geophysical logs, geologic interpretation, bore design, closed-loop mud system design, drilling and installation, waste management, bore disinfection, bore development, aquifer pump testing, daily reporting, weekly safety reporting, and finally, documentation of project deliverables. - That list sounds even more intimidating now than it did during the program.
From the beginning, Hunter Water had stressed great concern for the approaching wet weather season and the numerous access issues and delays that would be incurred. The entire site consisted of loose coastal sands and the existing access tracks were often in poor condition. Numac had selected a 38 ton EDM 2000 rig mounted on an 8x8 Man all terrain truck for the project. Although our EDM is a very capable off-road vehicle, the soft bottomless sands on this site would quickly become treacherous once we broke the surface. With the ever-present risk of significant rain as we moved through autumn into the winter months it was increasingly vital that Numac maintained solid progress from the start through to completion.
Our first technical hurdle on this program materialised before we even signed the final contract. The contract prohibited the inclusion of any bentonite products in the drilling fluid. We were not provided with any background on this specification and could only assume that a previous poor experience with a drilling contractor resulted in bentonite being framed as the culprit for the poor bore production. Some intense consultation with industry "experts “ensued as our client pushed hard for finalisation of the contract.
Our understanding of the formation was limited to some poorly detailed 50-year-old bore logs that indicated primarily flowing sands. Bentonite is the industries ‘go to drilling additive’ in sands formations, ensuing that you create a wall cake, increase specific gravity of the drilling fluid, and ultimately keep the bore open throughout the drilling and installation. Pre-mobilisation Numac’s senior drillers worked with drilling fluid suppliers to create a mud program that was adequate as there was no silts or clays in the formation. We worked constantly over the first couple of bores to refine the “mud ingredients” and to our great relief before long we had a sustainable mud formula that was working perfectly in the conditions.
To alleviate Hunter Water’s greatest concern – their project delivery would be delayed significantly due to site access related to wet weather, Numac had devised a plan to expedite the schedule by immediately drilling pilot holes for each supply bore upon completion of the drilling pad preparations We deployed an additional crew to run our sonic drilling rig. The plan had many benefits. The client would receive the lithology from a continuous core of the sand formation, allowing for the first time at Hunter Water a full vertical profile on each supply bore in the regional aquifer. The resulting core enabled development of the perfect well design. Screen placement with such a quality sample could be targeted down to the cm. All bores varied slightly in depth and design to match the subtle variations in the vertical profile. Had we used mud rotary techniques to drill the pilot bores the low-quality sample would have forced a more generic construction with potential negative effects production capacity.
The production well construction was a combination of 8" and 10" (200-250 mm) full stainless steel. Proposed drilling diameter of 16" (350 mm) would ensure a thick filter pack would providing excellent near well permeability, long turn pumping efficiency and low wear on pump components. Each 25-30 m bore would take a massive 2500 L of graded sand for its filter pack.
Drilling commenced with the EDM 2000 approximately a week after the Sonic sampling started. The bores were cased with 18" steel down to 6mbgl to ensure that there were no washouts at the surface.
Given the relatively shallow depth we utilized high volume centrifugal pumps sets with high solids capacity. The high solids capacity was important as we were not planning on using any solids control systems in the fluid system. In this case, we were able to use large above ground tanks to circulate enough drill fluid to complete a bore with a single mix. The cost advantage of setting up solids control in this instance was negated by the small-bore volumes.
Well installation required the welding of 6 m stainless steel lengths. The logistical challenges of moving such large sections of screen and casing to the bore locations was solved with a small tele-handler. The tele-handler was also utilized to assist with the 1.5 ton bags of filter pack material.
Given that rod handling (a significant manual handling risk) was completely eliminated on the rig, hoisting the screen and casing was by far the highest risk activity undertaken across the project. Project specific lifting tools were engineered for each of the well diameters and independently load tested and certified prior to mobilization.
Traditionally, when subcontracting to consultants Numac has to quote and execute projects around the logistical constraints imposed on us. Often, we feel that our equipment is heavily underutilized during its time on site resulting unnecessary costs. As the principal contractor, Numac had the opportunity to execute a drilling program where all variables were within our control. Where we were able to focus on the rig achieving maximum drill hours.
We began by ensuring that all preliminary and supplementary works were completed immediately. Any works that could hold up drilling later were attacked. Site access, underground utility service location, drill pad preparation, mud pits, pilot holes, wire-line tests geophysical and lithological logs were completed before the EDM our specialist large diameter water bore rig had arrived on site. When we commenced drilling, waste contractors were scheduled and waiting to empty our above ground mud system the minute each bore was finished. This allowed us to mobilise to the next site without delay. Having the rig mobilised off the bore allowed Numac to complete the bore disinfection and development immediately after the rig move, by utilising a second team. Concurrently the drilling team completed the rig set up, surface casing install, drilling mud and fluids preparations. This was a huge time saver at the each location enabling the rig to commence drilling immediately upon setup. Numac engaged and supervised a subcontractor to complete multi stage pump testing which we scheduled at a time that would ensure cost savings and efficiency for the contractor. The pump testing commenced half way through the program ensuring the tests could run consecutively, saving mobilisation charges and scheduling conflicts (i.e. money and time), allowing full weeks to be utilised.
Another major win for the drill rig utilisation was our accepted contract change request to alter the Hunter Water mandatory working hours to the original work-scope; from a 5 day to a 7-day work week. This greatly improved efficiency in that we could swap crews out on 2 week rosters without losing half days each Monday and Friday or being forced to stop drilling early because bore holes could not be left open over the weekend without risking collapse.
Suffice to say that gains made by having control of our own schedule were massive, it was a buzz to see a project progress so smoothly. Project completion was a month ahead of our projected schedule and significantly within the maximum timeframes permitted by the contract. The achievements of the project team cannot be understated and for the company. Surpassing what our client regarded as a nearly impossible deliverable schedule without sacrificing safety, quality and environmental responsibilities, is certainly one of our proudest moments.